Industry 4.0
Industry 4.0 Digital Twin
Industry 4.0 transformation, a pivotal component of which is the Industrial Internet of Things (IIoT) technology, combined with operational applications and analytics, enables higher quality and more efficient manufacturing processes.
DADATech’s developed Industrial Internet of Things and Manufacturing Analytics Platform, Dada360, allows you to create a “digital twin” of your manufacturing facility to carry out production processes in a rapid, efficient, and cost-effective manner, giving you a competitive edge.
With DadaT, we integrate data, IIoT, and AI-driven Industry 4.0 technologies with domain expertise. DADATech supports every aspect of the industry’s journey from vision to value:
- Strategic Consulting: Our industrial consulting teams develop tailored transformation roadmaps based on identified values and challenges.
- Secure Connectivity Infrastructure: We establish secure and efficient connectivity infrastructures tailored to manufacturing needs.
- Automation Integration: Our competent field teams ensure that automation equipment is connected and integrated.
- Digital Twin Implementation: We facilitate the creation of digital twins for manufacturing operations, enhancing monitoring and decision-making.
- Efficient and Quality Manufacturing: Managed with IIoT and advanced analytics, we aim to optimize production for better efficiency and quality.
DADATech is dedicated to delivering these solutions, leveraging advanced technologies to help manufacturing facilities modernize operations and thrive in the competitive landscape of Industry 4.0
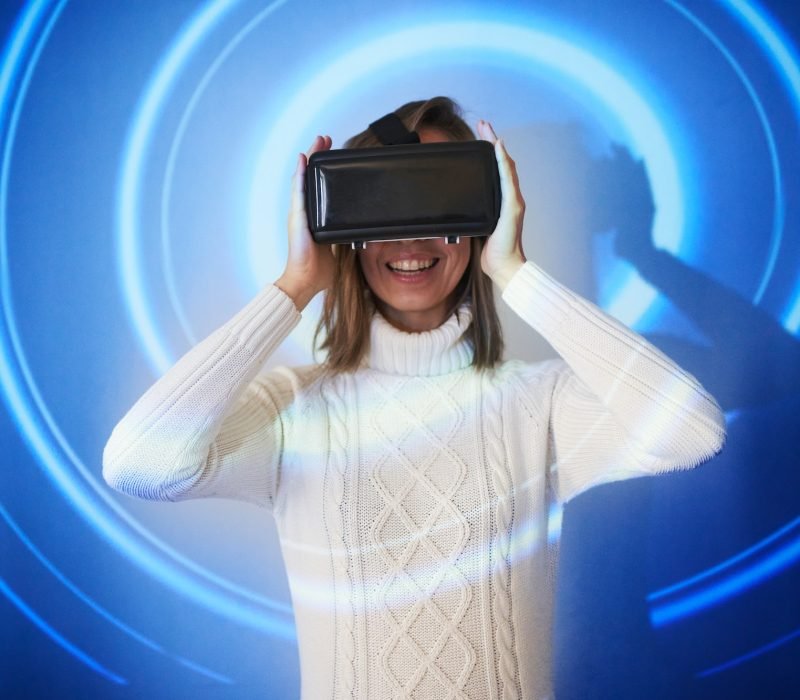
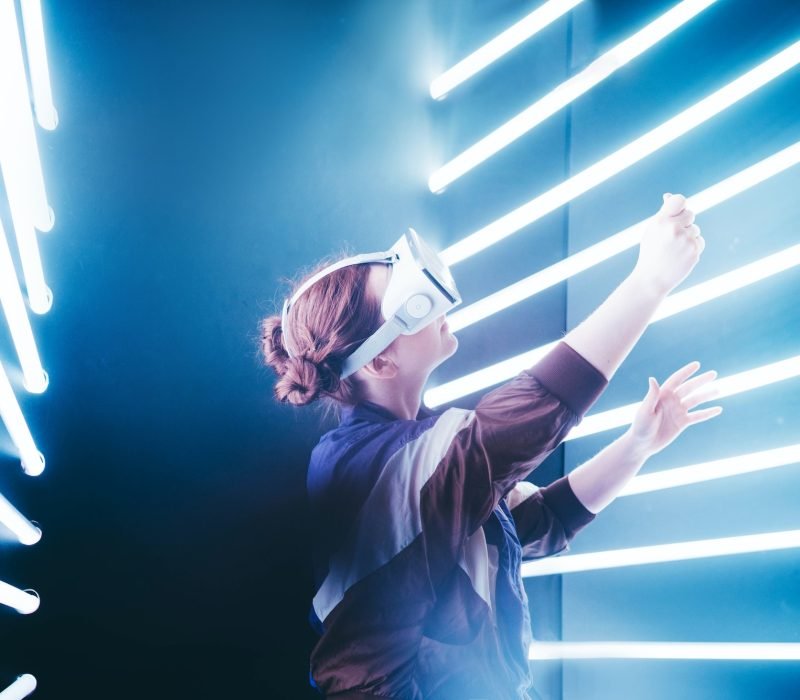
Digital Twin
The importance of smart data management and digital continuity is paramount in operations where businesses must rely on the quality and accuracy of the information gleaned from their processes. Nearly all the gains to be achieved in advancing processes are contingent upon the data being consistent and verifiable. Using engineering data, you can seize opportunities to optimize operational processes or, through maintenance activity data, identify potential mechanical failures before they occur and take preventive measures. Alarm data can pinpoint risky and critical processes, allowing for preemptive action against potential safety hazards.
Transform industrial and engineering data into operational insights, empowering operational teams to act proactively with these insights and maximize the return on investment (ROI) from critical assets.
Whether entrepreneurial or corporate, companies that successfully implement effective and smart data management will not only realize cost savings but will also harness the transformative impact and benefits of Digital Twin technology.
How can smart engineering leverage master data management to transform operational decision-making processes?
In the face of increasing global competition and erratic market conditions, businesses in the Oil & Gas, Chemical, Energy, Pharmaceutical, Mining, and Food industries are turning to digitalization solutions that can elevate their operational efficiency and performance, yielding swift and substantial returns from continuous improvement and optimization activities. However, innovation processes bring their own challenges. In the digital transformation processes brought by Industry 4.0, companies often encounter difficulties in collecting, storing, and evaluating the vast amounts of data generated by new tools, platforms, and sensors. Finding themselves in an ever-expanding sea of data, businesses are seeking digital transformation solutions that allow them to make accurate predictions and act rationally.
Smart integrated engineering systems are software that provides significant competitive advantages in leading engineering, procurement, and contracting projects. These systems offer efficiency improvements, time and cost savings, and also provide users from different engineering disciplines the opportunity to work together on a synchronous and shared platform.
Smart management of engineering data is at the heart of every digitalization project and is fundamental to a successful digital twin strategy.
A digital twin is a data and information representation of a physical object. It reliably reports the current status and behavior of assets using live IoT data and sensor information. With unparalleled levels of detail and analytical capabilities, a digital twin can become a decision-support tool that allows you to predict upcoming events and make forecasts about them. In other words, a digital twin can predict potential failures of its physical counterpart before they occur and suggest ways to prevent these errors.
However, a potential flaw exists. A digital twin is only as good as the detailed engineering master data it is built upon. Additionally, if a digital twin has access to detailed and verifiable information about the systems, areas, units, and rooms it represents, it can depict a situation that an engineering team can rely on.
What does digital continuity mean in the context of a digital twin, and how can it best be achieved?
There is a need for digital continuity throughout the lifecycle of an asset. This means that a real digital twin requires a series of core services to provide effective forecasts throughout the operational duration of a project.
Digital continuity is the foundation of an effective digital twin. Leaders in the field of digital continuity continue to uncover new values for flawless data usage throughout the asset lifecycle, while digital twins are no longer just a hot trend at the innovation forefront but are fundamental for guiding predictive maintenance, IIoT, and more advanced operational excellence programs.
What is the foundation of a digital twin?
Taking maintenance optimization as an example, it combines Asset Performance Management (APM) with predictive analytics, Enterprise Asset Management (EAM) with maintenance scheduling, 3D visualization with situational awareness, and detailed engineering data.
This information is presented in a work package as shown in the diagram above. Now, the maintenance manager can see performance and stress points, detailed design work at a glance, and use this information to predict potential challenges or opportunities for the facility.
To create an effective digital twin strategy, each asset creates its own set with master engineering data, effective visualization tools, and workflow procedures. The diagram above demonstrates the depth and breadth of data flows, giving an idea of the services that should be present in the digital twins of assets across various industries.
An effective digital twin synthesizes these data flows deeply and broadly, seamlessly implementing core business processes using technological capabilities, and ensuring data is integrated into computer-based analyses that are cost-effective, ready-to-use, and high-performing.
As behaviors change along with technology…
Showing the power of a digital twin on a screen is easy. Achieving meaningful operational efficiency gains, improving safety performance, and reducing costs requires a different way of thinking about and interacting with data and the asset itself. It also requires a change in the mindset of business owners and operators who previously saw digitalization investments as optional expenditures.
The rise of the digital twin requires companies to create comprehensive digitalization strategies that require guaranteed, reliable digital engineering master data to be protected and managed throughout the asset lifecycle. This situation emerges as much a technological issue as it is a cultural and human process challenge. However, the transformation processes that industry leaders are now undertaking with increasing urgency and seriousness are no longer seen as a challenge but a necessity.
Smart data management becomes central to success.
When these intelligent systems are combined with a central platform that archives and provides access to data throughout the lifecycle of an asset in a complex investment project, the company achieves results that enhance its competitive edge. What a digital twin needs to be effective is exactly this kind of long-term, smart master data management.
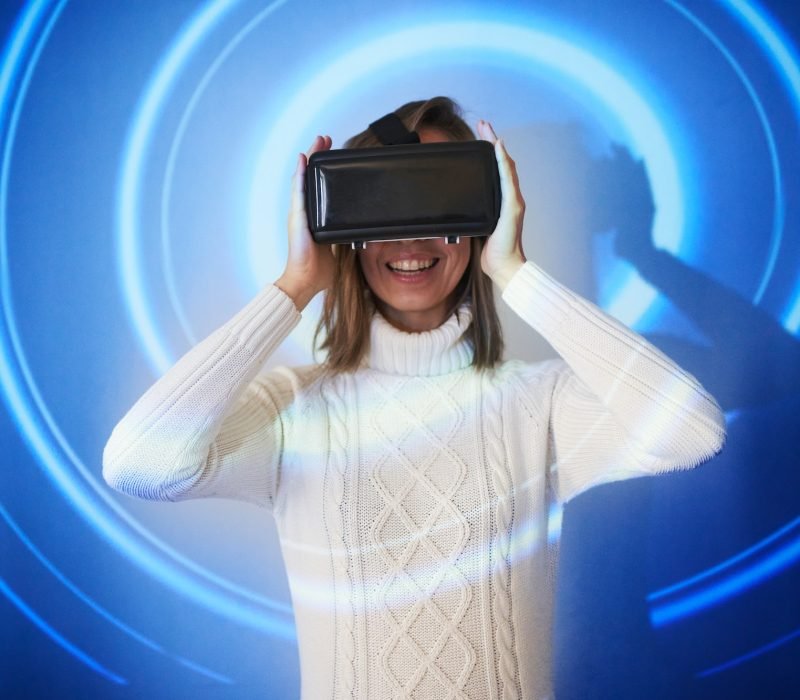
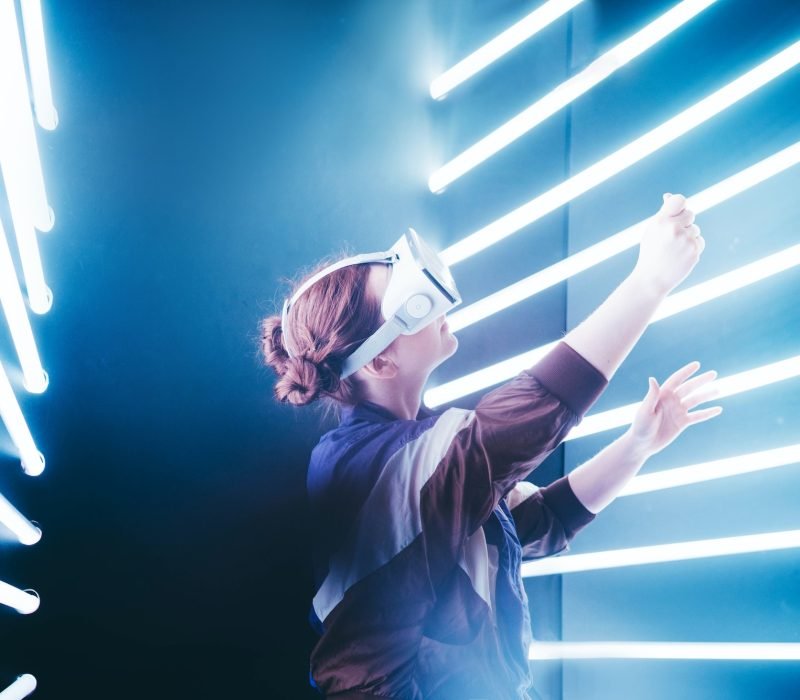